You may have heard the joke… “Who’s driving digital transformation at your company: the CEO, CIO, or… COVID-19?” Besides unleashing a wave of video conferencing and remote desktopping, COVID-19 has indeed stimulated accelerated adoption of certain digital technologies, such as remote monitoring, remote assistance, and even remote or independent training using augmented and virtual reality. But most companies are barely scratching the surface of what seems to be quickly becoming possible through some of the most promising emerging technologies.
After the mechanization, electrification, and computerization of the first three “Industrial Revolutions”, the time has come for connected and autonomous machines (aka “Cyber Physical Systems”) to start making their own decisions, fueled by a plethora of data and machine learning algorithms. And for “connected workers” to make better decisions and achieve ever higher levels of safety, quality and productivity thanks to detailed, integrated, accurate, and up-to-date information. At least that is the vision more and more companies are working towards.
South Carolina has a proud history in manufacturing. Once focused on textile mills and apparel jobs, we now make the world’s best cars, tires, planes, and many other high-value and complex products, right here in our Palmetto State.
Driving significant foreign direct investment, major exports, and thousands of well-paying jobs, manufacturing clearly plays a very important role in our economy and in many people’s lives.
Across our great state, South Carolina manufacturers -large and small- are working hard every day to maintain and increase their competitiveness through process improvement, employee training, and increasingly: applying “Advanced Manufacturing” technologies and practices. But what exactly is “Advanced Manufacturing”?
According to a 2013 report by the National Association of Manufacturers, “Advanced Manufacturing techniques improve manufacturing processes and products through the use of innovative technologies, such as automation, computer technologies, process technologies and information technologies, control systems, high precision technologies, sustainability technologies, and advanced robotics”.
So, according to the above definition, “Advanced Manufacturing” is focused on taking advantage of the best manufacturing technologies and techniques available, including a number of “emerging” technologies. While CAD and CNC-driven machines, robots and lasers were major drivers for the “Third Industrial Revolution”, the focus of the “Fourth Industrial Revolution” is on a new set of technologies, including Additive Manufacturing (more commonly referred to as “3D printing”), the Industrial Internet of Things, real-time (“advanced”) analytics, and machine learning.
Fourth Industrial Revolution, Industry 4.0, Advanced Manufacturing, Smart Manufacturing, Factory-of-the-Future, Industrial Internet of Things, Cyber-Physical Systems… it’s challenging to make sense of it all. For all practical purposes, it’s probably safe to use “Advanced Manufacturing” and “Industry 4.0” interchangeably. And the same goes for “Smart Manufacturing” and “Factory of the Future”.
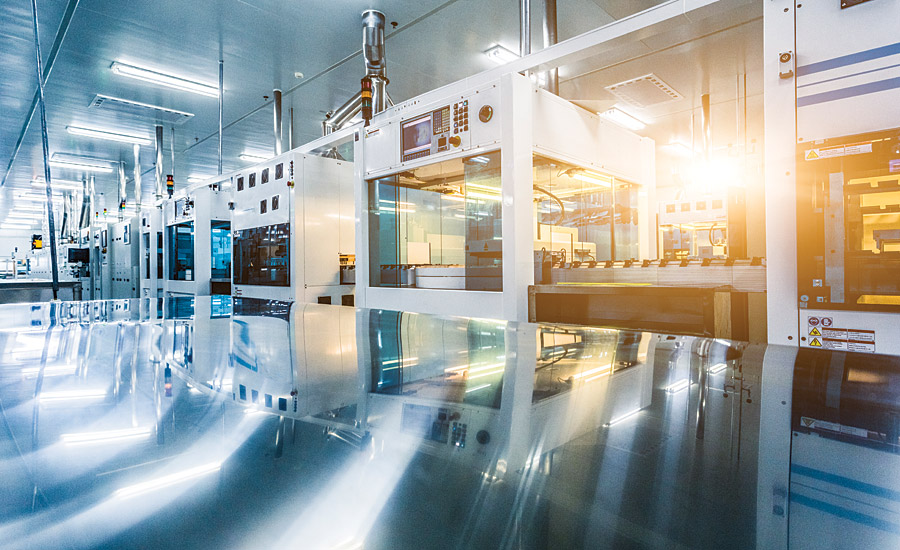
Factory of the Future
Many people also use the term “Internet of Things”, or more specifically: “Industrial Internet of Things”, but that’s really just a subset of the very wide range of technologies involved in Industry 4.0.
Besides the sensors, connectivity, and cloud computing involved in the (Industrial) Internet of Things, Industry 4.0 also involves edge (and even “fog”) computing, additive manufacturing, smart robots and cobots, digital twin, digital thread, augmented reality, virtual reality, simulation, blockchain, robotic process automation, computer vision, advanced analytics, machine learning, artificial intelligence, and many more.
The sheer number of technologies and terminologies involved is rather bewildering.
Whatever the terminology and specific technologies used, there seems to be one common theme: data as the “new oil”. Process operating parameters, product quality characteristics, and even environmental variables such as temperature, humidity, etc. are being tracked with ever increasing granularity, using a growing array of smart connected sensors, up to the millisecond level and beyond.
Besides monitoring product quality, process performance, and equipment condition, operator data is being measured in ever greater detail as well, for analysis and decision-making around productivity, quality, safety and ergonomics. All this data holds the potential for significant further process improvement, as long as we find an efficient and reliable way to “clean”, validate, integrate, and analyze it all. And then present -and visualize- the insights gained in an understandable and actionable manner. Good old Excel, by itself, will no longer cut it. That’s where Advanced Analytics, Machine Learning and Artificial Intelligence come in.
We’ve mentioned a whole bunch of different technologies so far. But, Industry 4.0 and Advanced Manufacturing are about much more than technology. Ultimately, it all starts and ends with people and processes, as the goal is to enable (empower!) people to run better processes better – and make higher-quality products faster and cheaper. It does not matter how powerful a certain technology is, if it does not solve a specific problem or provide some measurable and relevant benefit. Technology for the sake of technology is just another form of waste. It all sounds pretty obvious, but it gets forgotten too easily at times, especially when the (Corporate?) pressure is on to “digitize operations”.
Time for another buzz term: “Digital Transformation”. Industry 4.0 concepts are typically at the core of digital transformation initiatives in manufacturing environments. In reality, some companies talk a good game about “digital transformation” when all they are really doing is implementing -or even just experimenting with- a couple of digital technologies. Nothing wrong at all with experimentation and learning, of course, as we all could use much more of it. But true digital transformation goes way broader and deeper than that, as true digital transformation really is business transformation enabled by digital technologies.
Which implies fundamental change in how a business is being run, including processes and systems, but also e.g. organizational structure and talent management. And even strategy, as emerging technologies may pose new threats or opportunities, and enable new ways to generate and capture value. (Ultimately, certain breakthrough capabilities provided by certain emerging technologies may even trigger organizations to reconsider their whole focus and purpose.)
It should come as no surprise that Industry 4.0 initiatives can be rather challenging. How to prioritize the best use cases and select the most promising technologies? How to realistically assess costs and benefits to justify the investment? How to find and select the right solution vendors and partners? How to successfully get things implemented and integrated? How to upskill current employees and/or attract fresh talent? How to deal with data protection and cyber security concerns?
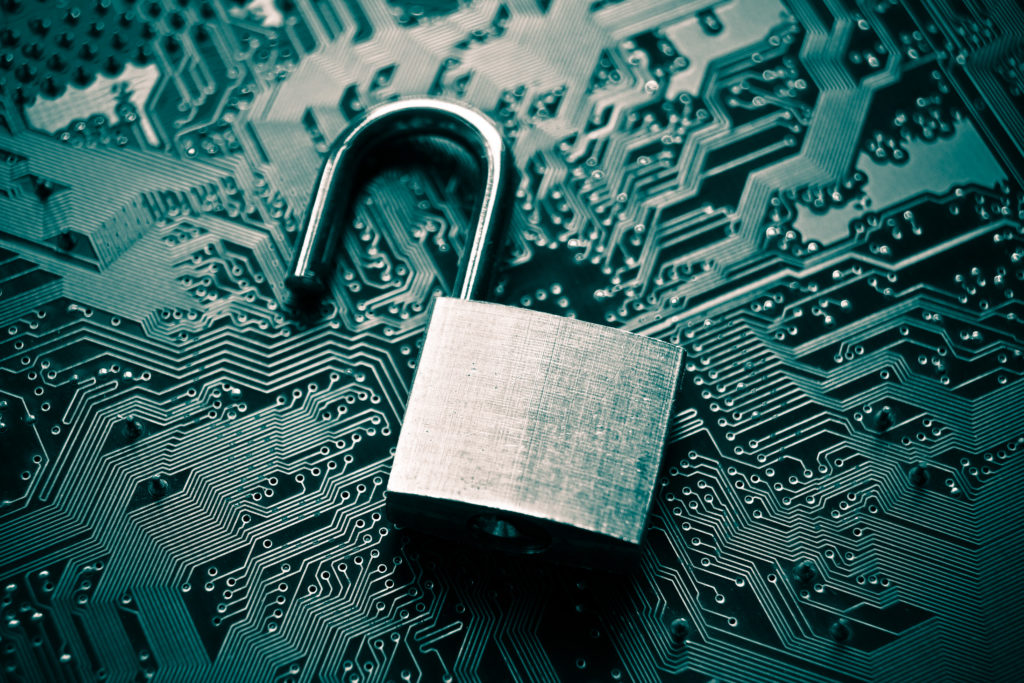
Cyber Security
The impact of Industry 4.0 technologies on the people and processes involved can be very significant. Is supposed to be very significant, actually. Which can lead to anxiety and pushback, rather than excitement and adoption. And, if implementing a few specific Industry 4.0 technologies is challenging already, actual digital transformation takes scale and complexity to the next level.
It does not help that many of the technologies involved remain “emerging”, i.e. not widely adopted and sometimes unproven. See Gartner’s “Hype Cycle for Emerging Technologies”. If so much of it may be hyped, possibly even fad, then why bother? Why take the risk?
First off, the promise is significant. It’s not easy to get reliable and relatable information on performance improvements gained through the implementation of specific Industry 4.0 technologies. But the improvements being reported by independent sources are typically in the double digits. Imagine being able to reduce equipment downtime, cost-of-quality, inventory levels, maintenance cost, etc. with 10 – 20 – 30%. Now imagine your competition being able to achieve those levels of improvement. Not acting doesn’t seem like much of an option.
We are talking about global competition here, by the way. The term “Industry 4.0” was coined in Germany, and Europe has many initiatives, both at the country level and at the European level, to help its manufacturing base take advantage of new digital capabilities. And China is digitizing and automating at a rapid pace as well, with clear -and centrally controlled- strategic objectives to become a global powerhouse in cutting-edge manufacturing technologies such as artificial intelligence. Clearly, we are in a global race, with significant upside potential… and far-reaching consequences in case we’d fall behind.
At the very least, every manufacturing company in South Carolina should be aware of the most promising digital technologies out there. Especially those that are reaching some level of practical and affordable maturity. And most importantly: those that are delivering real, tangible bottom-line benefits and results.
Everyone involved in running South Carolina manufacturing companies should have a basic understanding of Digital Transformation and how best to approach things.
So, in the coming months, we will be writing a series of posts about specific Industry 4.0 technologies as well as broader digital transformation aspects. Our goal is to inform, educate, and hopefully inspire more South Carolina manufacturing companies to get started with digital transformation using worthwhile (“non-fad”) Industry 4.0 technologies.
We will be taking both a bottom-up and top-down approach, sharing (hopefully) insightful and useful information from a higher-level perspective, incl. the people, process, and even some strategy aspects, while also covering specific technologies: what is it? what does it do? how does it work? what are the main use cases and benefits? what are the downsides and risks? what are the alternatives?
As much as possible, we will try to leave out the fluff, buzz, and bs.
We will be sharing personal experiences from working with our manufacturing clients on a range of initiatives. And we will also be reading up and researching to further enhance our own knowledge, understanding, and ability to share. This is a very broad and fast-moving topic, of course, and there’s only so much we can know and keep up with ourselves. So, we invite anyone interested to reach out and contribute. We’d love to hear from you! Please let us know which specific topics or aspects of Industry 4.0 and digital transformation you’d like to learn more about, or any insights or experiences you are willing to share, so we can incorporate things in future posts. Based on our combined experience, expertise, and ideas, we can help manufacturing in our State thrive and prosper for many years to come!
–
About the Author:
Stijn (“Stain”) Van de Velde is CEO of Gemba Systems Inc. and Managing Partner of Execution Partners LLC, both located in Greenville, SC. While Gemba Systems focuses on the introduction and implementation of specific Industry 4.0 technologies, Execution Partners typically takes a more strategic approach, guiding and assisting companies along their digital transformation journey. As a dual citizen with Belgian roots, Stijn serves as the liaison to Greenville’s Belgian Sister City, Kortrijk, and also supports the Belgian Consulate in Atlanta as an Advisor for Economic Diplomacy. In his spare time, he enjoys reading, biking, and hiking the Carolina mountains with his wife, son, and dogs.
Be the first to comment on "Advanced Manufacturing using Industry 4.0 technologies"