SUVs tip the scales at about 4,000 pounds, but they could soon shed some weight with the help of a nationwide team led by a Clemson University automotive engineer.
The team is launching new research aimed at knocking at least 160 pounds off of an SUV while maintaining affordability and ensuring automakers can mass produce it without retooling their facilities.
A lighter vehicle requires less energy to travel. The idea is to reduce the amount of fossil fuels burned in gasoline- and diesel-powered vehicles and increase the range of electric vehicles.

Srikanth Pilla (center in the purple mask) is principal investigator on project aimed at reducing the weight of a Honda SUV.
To fund the project, researchers are receiving $5.75 million from the U.S. Department of Energy Office of Energy Efficiency and Renewable Energy Vehicles Technology Office. Various partners will share the cost, bringing the total expected funding to $11.5 million.
The team will focus on what looks like the skeleton of the SUV and is interchangeably called the glider or body-in-white. A big part of the challenge will be incorporating a wide range of materials, including various metals and carbon-fiber-reinforced polymer composites, and figuring out how best to join them together.
The principal investigator on the project is Srikanth Pilla, the Jenkins Endowed Professor of Automotive Engineering and founding director of the Clemson Composites Center.
“The main question that we are trying to tackle is, ‘Are there technologies that we can bring together and come up with an integrated concept in which we can lightweight a body-in-white?’” Pilla said. “If we take away 160 pounds, it will enable energy savings and help achieve decarbonization.”
Researchers want to meet their weight-saving goal without increasing the cost of the glider more than $5 for every pound saved. They are also setting out to ensure that manufacturers would be able to make 200,000 of the gliders per year without a major retooling or investment in capital equipment.
The team will use a glider from a 2019 Honda Pilot for the study, but the results are expected to apply to a broad range of vehicles.
While automotive components made from carbon-fiber-reinforced polymer composites are light and strong, incorporating them into vehicles often requires expensive changes to how the vehicles are manufactured.
One of the project’s collaborators, Marcelo Dapino, has been working on this challenge and will bring his technological advances to the new research. Dapino said his lab previously worked with Honda to develop a technology for joining carbon fiber to metal.
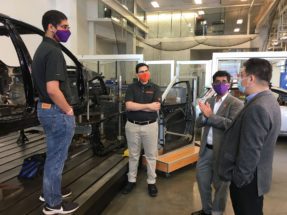
From left: Aditya Pradeep, Amit Deshpande, Srikanth Pilla and Gang Li work in a lab at CU-ICAR. Read more about the experience graduate students will get from participating in the SUV research here.
“We can create carbon-fiber-reinforced polymer structures with metallic tabs or attachment points,” said Dapino, who is the Honda Designated Chair in Engineering at The Ohio State University.
“Those metallic tabs allow the carbon fiber structure to be welded to the rest of the vehicle. The key advantage to Honda and automotive manufacturers in general is they can spot-weld carbon fiber structures to the rest of the vehicle without changing the infrastructure of the manufacturing facility.”
Ryan Hahnlen, a senior research engineer at Honda Development and Manufacturing of America, said that for the new project, Honda will provide a mass-production vehicle, performance goals and guidance to researchers. It will be important to ensure the new design does not compromise the current design’s performance and that the new design can be integrated into existing production environments, he said.
“This project offers the opportunity to look at the vehicle structure holistically,” Hahnlen said. “It also allows us to take full advantage of composite properties while improving cost and manufacturability aspects. I’m most excited about taking advanced materials and methods that have demonstrated benefits at part- and system-level research applications and applying them at full-vehicle scale to better understand their full benefit potential.”
Gang Li, a professor of mechanical engineering at Clemson, will create a digital lifecycle for the glider. As part of the digital lifecycle, researchers will employ advanced modeling techniques to replicate on computers what happens in the physical world.
“We are looking at the physics in every step from manufacturing all the way to the actual performance on the road,” Li said. “We will also look into the structure. We will look at microstructures of the material and understand how these microstructures will affect the material properties and performance in the actual product.”
The approach will help save money and accelerate the glider’s development and optimization, Li said. Digital tests can be done less expensively and more quickly than testing physical components.
Research team members come from eight organizations in addition to Clemson, Ohio State and Honda R&D Americas. They are: MSC Software Corporation, Altair Engineering, Moldex3D North America, Inc., Siemens USA, Proper Tooling, Carbon Conversions, Huntsman Advanced Materials and ZOLTEK Corporation.
The project is the latest collaboration involving Pilla and Honda, with funding from the Department of Energy. In previous research, Pilla and his team worked with Honda to design and make a prototype of an ultra-lightweight door using carbon-fiber-reinforced thermoplastic. They found a way to reduce the number of structural parts from 17 to eight.
Zoran Filipi, chair of the Department of Automotive Engineering, said Clemson is well equipped to lead the new research.
“Dr. Pilla’s past success in conducting research in the area of lightweighting, his collaborations with industry and his experience in assembling large, nationwide research teams makes him uniquely qualified to lead this project,” Filipi said. “Clemson also brings to the project world-class facilities and top students. The team is well positioned for success.”
Anand Gramopadhye, dean of the College of Engineering, Computing and Applied Sciences, congratulated the team on the grant.
“The level of funding is a testament to its importance in shaping the future of transportation to support federal decarbonization efforts,” he said. “With this project and many others, the college is establishing itself as the nationwide leader in automotive research.”
Read more about the experience graduate students will get from participating in the research here.
Be the first to comment on "SUVs could soon go on a carbon-fiber diet"